Food Packaging Process Solution - Integrating High-Volume Products with Flow Wrappers
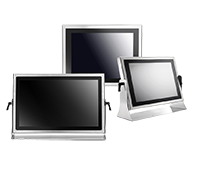
Background In the food packaging industry, the need for efficient and reliable packaging solutions is paramount, particularly when handling high volumes of products. Flow wrappers are widely used in the industry for their ability to package products quickly and consistently, maintaining product freshness and extending shelf life. These machines are designed to wrap items in a continuous flow, making them ideal for high-speed production environments. However, the increasing complexity and volume of products being processed demand more advanced control systems to ensure seamless operation and minimize downtime.
Pain Points As the demand for high-volume packaging grows, traditional Human-Machine Interface (HMI) systems often struggle to keep pace with the needs of modern flow wrappers. Operators require intuitive and responsive HMIs that can handle the complexities of automated packaging systems. The pain points typically include: 1. Complexity of Control: Managing multiple packaging variables simultaneously, such as product size, speed, and wrapping material, requires a sophisticated HMI that can simplify these controls for operators. 2. Real-time Monitoring and Adjustments: High-speed operations demand real-time data and the ability to make quick adjustments to prevent errors or material waste, which many standard HMIs are not equipped to handle effectively. 3. Integration with Existing Systems: The need to integrate HMIs with existing factory systems, including upstream and downstream equipment, can present challenges, especially when compatibility and communication protocols vary. 4. Reliability and Maintenance: In high-volume production environments, any downtime due to HMI failure can be costly. Therefore, HMIs must be robust, with easy-to-navigate maintenance features that reduce the risk of extended interruptions.
Wincomm Solutions
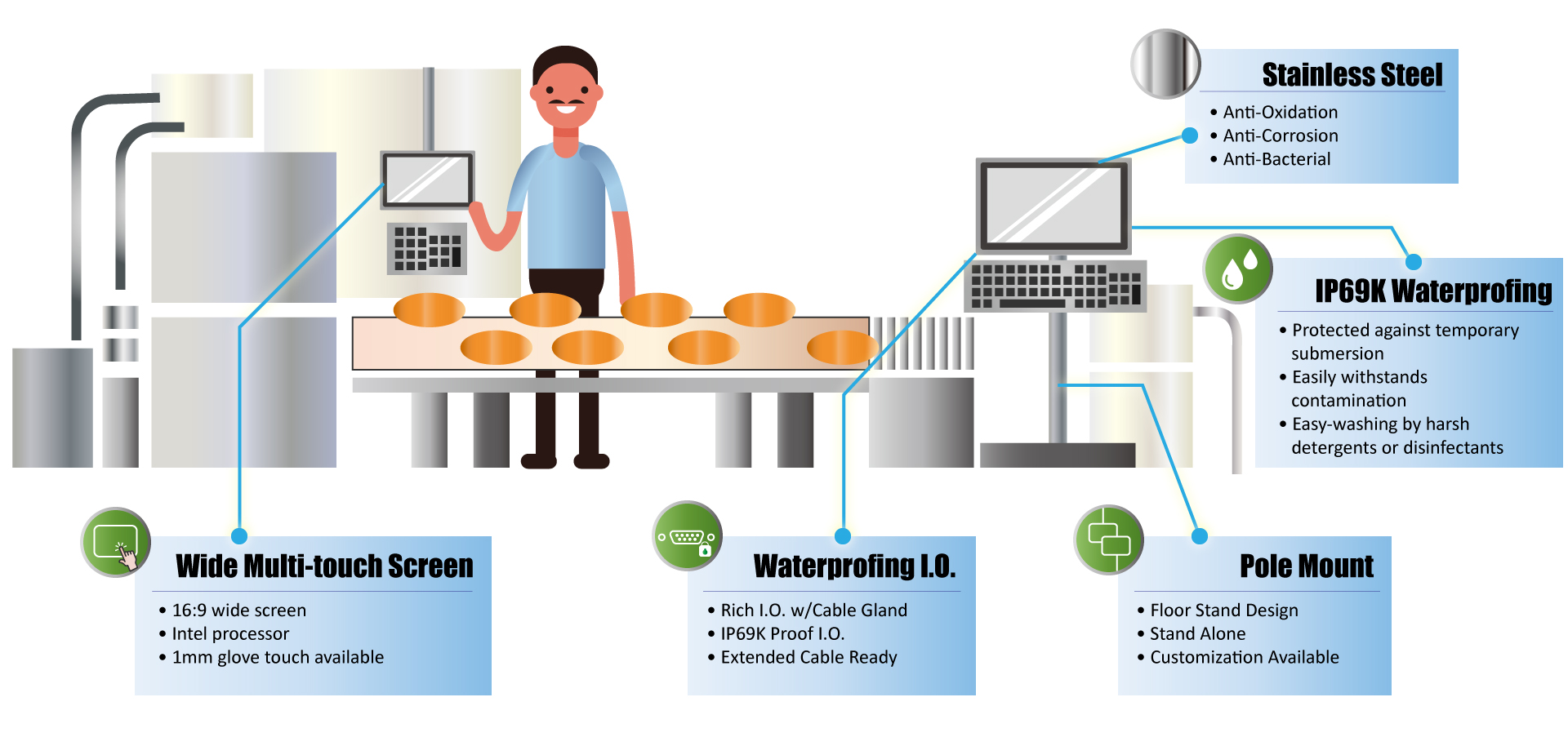 To address the demanding requirements of high-volume food packaging environments, Wincomm’s WTP series of full IP panel PCs offer a robust solution. These panel PCs feature stainless steel housing and are certified IP69K waterproof and dustproof, ensuring they can withstand rigorous cleaning processes involving water, harsh detergents, and acidic or alkaline disinfectants at temperatures up to 80°C and pressures up to 30 Bar.
Designed for versatility, the WTP series supports floor stands, ceiling mount, customized integrated housing and wash-downward I.O. to support machine control. All I/O outputs are IP66 certified, ensuring reliable performance even in the harshest conditions. For installations with physical constraints, Wincomm offers extension cables to overcome these limitations. In response to specific environmental requirements, the WTP series also supports wide-screen displays with a 16:9 aspect ratio, available in sizes ranging from 10.1" to 23.8". This flexibility ensures that operators have clear, easily accessible information at all times, enhancing the overall efficiency and reliability of the food packaging process.
If you have any product or customization requirements, please contact Wincomm sales (mail: sales_support@wincomm.com.tw). For more product information, please visit the Wincomm website at http://www.wincomm.com.tw/
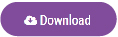
Related Products
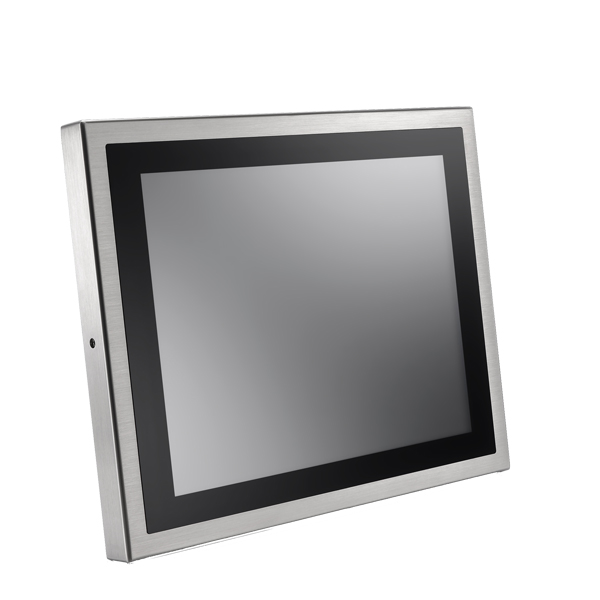 |
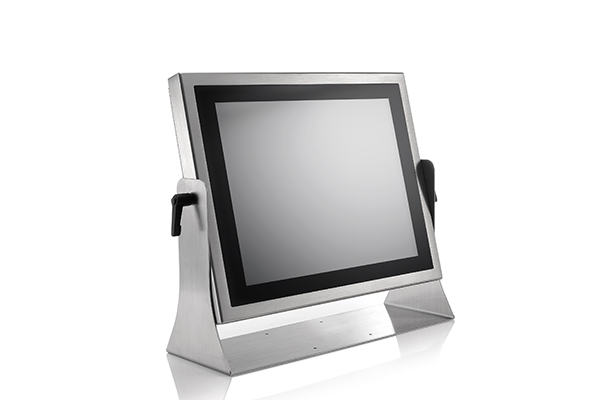 |
WTP-9H66 Series |
WTP-8J66 Series |
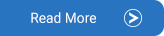 |
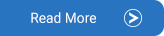 |
|